In the world of PCB assembly, the
pick and place machine plays a pivotal role in ensuring speed, consistency, and precision. Even highly advanced systems are still susceptible to occasional operational disruptions.These issues not only reduce throughput but also increase defect rates and rework costs. This article explores some of the most common problems in pick and place machines, why they happen, and how to effectively fix them—backed with real data and cross-comparisons to improve overall production efficiency.
Component Misplacement in Pick and Place Machines
Causes of Inaccurate Placement
Component misplacement is one of the most frequent issues encountered in pick and place machine operations, especially when placing components smaller than 0402.
Key factors include:
- Misaligned vision calibration
- Nozzle wear or contamination
- Improper feeder positioning
Recommended Fixes:
- Regularly calibrate the vision system and gantry alignment (at least once per 50 hours of runtime)
- Replace nozzles after 500,000 picksor earlier if vacuum pressure drops
- Ensure feeder rails are cleaned and mechanically aligned
Error Type |
Root Cause |
Suggested Fix |
Lateral offset |
Camera misalignment |
Recalibrate with fiducials |
Component shift |
Vacuum loss or nozzle clog |
Clean/replace nozzle, check vacuum pump |
Tilted components |
Feeder reel tension error |
Adjust feeder position and tension |
Frequent Pickup Failures
Why the Nozzle Fails to Pick Components
Pickup failure can seriously disrupt the cycle time of a pick and place machine, especially at high-speed settings (>40,000 CPH). Vacuum-related issues are the primary culprit.
Typical causes:
- Inadequate vacuum pressure (should be ≥60 kPa for standard ICs)
- Incorrect nozzle selection for component size
- Tape cover misfeeds or feeder wear
Fixing Strategies:
- Monitor vacuum levels in real-time using system diagnostics
- Match nozzle IDs to part geometries and heights
- Replace worn feeders every 12–18 monthsdepending on usage
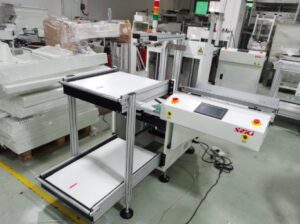
Feeder Jamming and Misfeeds
Material Handling Bottlenecks
Feeder problems account for up to 35% of unplanned downtime in medium-volume SMT lines.
Common symptoms:
- Misfed tape
- Delayed indexing
- Component drop due to feeder slippage
Solutions:
- Switch to smart feeders with feedback controls
- Schedule feeder maintenance weekly (especially in humid or dusty environments)
- Train operators to load and lock feeders properly—many misfeeds come from improper setup
Comparison: Manual vs Smart Feeders
Feature |
Manual Feeder |
Smart Feeder |
Setup Time |
~5–7 min per reel |
<2 min per reel |
Error Detection |
No |
Yes (sensor-based) |
Maintenance Cycle |
Frequent |
Predictive alerts |
Inconsistent Placement Speed
Diagnosing Line Bottlenecks
Even when running a high-speed pick and place machine, actual throughput often falls short of the rated speed (e.g., only reaching 70% of theoretical 60,000 CPH).
Reasons include:
- Poorly optimized part allocation across multiple heads
- Excessive travel distance between feeders and placement sites
- Overhead from vision verification time
How to Fix It:
- Use pick-and-place optimization software to balance workloads
- Reassign high-frequency components closer to center heads
- Shorten conveyor index times and synchronize with solder paste inspection feedback
Nozzle Wear and Maintenance Oversight
Hidden Downtime Risks
Nozzles may seem like simple parts, but even microscopic abrasions or dirt can lead to vacuum loss, poor pickups, and component flipping.
Signs of nozzle issues:
- Missing components on board
- High reject rate at AOI
- Vacuum alert warnings during operation
Maintenance Checklist:
- Inspect nozzles daily under 50x magnification
- Clean using ultrasonic baths every 2–3 shifts
- Replace nozzles showing signs of rust or wear at the tip
Keeping Pick and Place Machines at Peak Performance
To minimize downtime and ensure consistent output, every pick and place machine should be maintained according to manufacturer schedules while being monitored through MES or production dashboards.
Preventive Actions:
- Log daily machine status (CPH, errors, rejects)
- Use SPC (Statistical Process Control) for identifying performance drift
- Schedule monthly full line audits, especially for high-volume production
Conclusion: Prevention is More Efficient Than Repair
A pick and place machine is a complex system involving mechanical, pneumatic, and optical components. While it's tempting to chase higher speed or advanced features, real efficiency gains come from avoiding frequent faults, ensuring routine maintenance, and training personnel to identify early signs of malfunction.
When problems do arise, timely and targeted fixes are far more cost-effective than unplanned stops or quality failures down the line. For any SMT operation, reducing the top five failure modes mentioned above can improve yield by over 10%, directly impacting profit margins and customer satisfaction.
0