In electronics manufacturing, the speed, accuracy, and consistency of
SMT lines directly determine production output and cost efficiency. An under-optimized SMT line can result in bottlenecks, increased defect rates, and higher per-unit cost. Whether you’re running a high-mix, low-volume operation or a high-volume, low-mix factory, optimizing SMT lines is essential for staying competitive in today's fast-paced market.
Understanding SMT Lines in Context
SMT lines (Surface Mount Technology production lines) are the backbone of modern PCB assembly. A standard SMT line typically includes:
- Solder Paste Printer
- SPI (Solder Paste Inspection)
- Pick-and-Place Machine(s)
- Reflow Oven
- AOI (Automated Optical Inspection)
A well-optimized line can place up to 60,000 components per hour (CPH) with placement accuracy within ±0.035 mm.
Key Areas to Optimize SMT Lines for High Efficiency
1. Component Placement Speed and Accuracy
The pick-and-place process is often the slowest and most critical stage in SMT lines.
Optimization tips:
- Use multi-heador multi-gantry machines for parallel processing.
- Group similar components in feeder zones to minimize head travel.
- Regularly calibrate nozzles and feeders to maintain <0.05 mm
Comparison of Placement Configurations
Machine Type |
Typical CPH |
Accuracy (mm) |
Best For |
Single-gantry |
20,000–30,000 |
±0.05 |
Prototyping/Low Volume |
Dual-gantry |
40,000–60,000 |
±0.03 |
High-speed production |
Chip shooter + flexible |
60,000+ |
±0.035 |
Complex assemblies |
2. Optimizing Solder Paste Printing
Soldering defects account for 50–70% of all SMT line issues. Improving solder paste printing can dramatically reduce rework.
Strategies include:
- Use high-precision stencilswith nano-coating to prevent paste clogging.
- Monitor paste viscosity in real-time (ideal range: 800–1,200 Pa·s).
- Integrate SPI systems to immediately detect insufficient or excessive paste.
3. Line Balancing and Scheduling
One common issue in SMT lines is idle machine time due to unbalanced process steps.
Solutions:
- Run cycle time analysisto identify bottlenecks.
- Adjust feeder layouts to balance component distribution between placement heads.
- Implement inline buffer zonesbetween stages to reduce machine wait times.
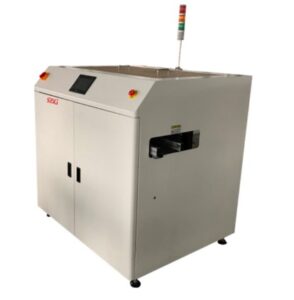
4. Inspection and Quality Control Integration
High-speed AOI and real-time defect analysis can prevent quality issues from reaching downstream processes.
Efficiency upgrades:
- Deploy AOI systems with machine learning defect recognition.
- Automate SPI-to-printer feedback loops for self-correction.
- Use closed-loop systems that feed data from AOI back to the pick-and-place programming.
5. Material and Feeder Management
Poor material logistics can disrupt otherwise high-performing SMT lines.
Recommendations:
- Introduce feeder trolleysto allow offline reel preparation.
- Use MES (Manufacturing Execution System) for material tracking and feeder position validation.
- Minimize reel changeover by using bulk feedersor multi-lane trays.
Cost and Efficiency Trade-offs in SMT Line Optimization
While full automation can improve output, ROI depends on your production model.
Factor |
High-Volume SMT Line |
High-Mix Low-Volume SMT Line |
ROI Timeframe |
12–18 months |
24+ months |
Automation Level |
Full automation preferred |
Semi-automation or modular |
Flexibility |
Lower |
Higher |
Changeover Time Importance |
Low |
High |
Understanding your production context is key—there's no one-size-fits-all SMT line configuration.
Additional Tips to Enhance SMT Line Efficiency
- Regularly review OEE (Overall Equipment Effectiveness). Industry targets are often:
- Availability> 85%
- Performance> 90%
- Quality> 99%
- Implement quick changeover protocols (SMED)to reduce downtime between product batches.
- Train operators on IPC standards (e.g., IPC-A-610) and empower them to resolve line stops.
Conclusion: SMT Lines Are Only as Efficient as Their Weakest Step
The most successful electronics manufacturers treat SMT lines not as individual machines but as interdependent systems. By optimizing equipment placement, data feedback loops, material flow, and quality control in tandem, factories can reduce costs, improve yields, and shorten delivery cycles.
In a production environment where a single line can handle millions of components per week, even a 5% gain in efficiency can translate to substantial cost savings and output growth. SMT line optimization is not a one-time task—it's an ongoing strategy critical to global manufacturing success.
0